Printing in Green and 3D
Basics of 3D Printing
Three-dimensional printing, also called 3D Printing, or Additive Manufacturing, is a process by which successive layers of materials are laid down under computer control to make a three-dimensional object. It is done by a 3D printer, a type of industry robot. The objects can be any shape and are produced from a 3D model or other electronic data source.
Originally developed in the 1980s, early 3D printing referred to the process of depositing layers of materials onto a powder bed with inkjet printer heads. More recently, the term has expanded to encompass a wide variety of techniques, including extrusion and sintering. The most obvious and immediate application of 3D printing is in prototyping. Using 3D printers, designers can quickly and easily translate plans into prototypes.
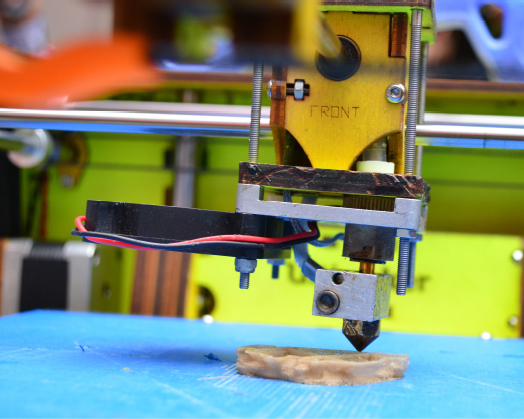
3D Printing as Sustainable Manufacturing Practice
Although 3D printing technology is not mature enough yet to fully replace all manufacturing, introduction of this method has revolutionized the manufacturing process. Currently only about 20 per cent of the output of 3D printers is final products rather than prototypes. However, the potential of producing everything from plastics and food to human tissues locally using a simple, compact printer has turned conventional concepts of manufacturing on their heads.
Traditional manufacturing methods focus on milling a material until you achieve a desired shape or injecting material into a mould. Both processes rely on expensive, high-volume machinery to achieve high economies of scale and at the same time minimize raw material waste. To achieve this, traditional manufacturing is generally performed at a production facility (a factory) and shipped around the world. Traditional manufacturing often means lots of emissions, which have a high impact on the local environment. And despite valiant attempts to minimize raw material waste, high waste volumes are still inevitable in mass production more often than we would like to see. In addition, the fuel cost of transportation also increases the cost of production.
By contract, in additive manufacturing, the product is printed one layer at a time, with each subsequent cross-section stacked on top of the previous one. This operation can be performed without huge, high-throughput machinery. This means that it can be carried out at hundreds or even thousands of sites at nearly zero waste. Thus, one can imagine a future where every household can have a 3D printer for use, producing objects quickly, inexpensively, and with minimal impact on the environment.
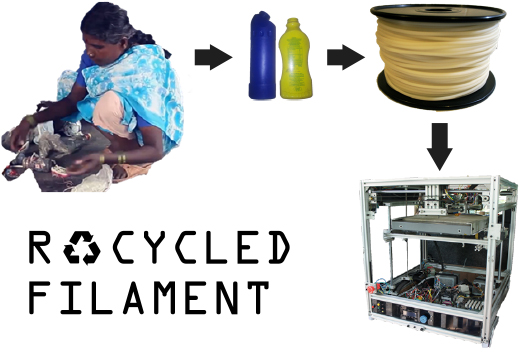
Turning Plastic Trash into 3D Printing Material
Given the benefits of 3D printing, why isn't it more popular? One limitation to making 3D printing more widespread is the high cost of the plastic filaments used in the printing—usually around US$35 to $50 per kilogramme. To overcome this barrier, a new initiative has been launched to lower the cost of the plastic filaments by utilizing recycled plastic. The potential savings of producing on a household-scale or lab-scale is remarkable if recycled filaments can be used.
Researchers at the Open Sustainability Technology Group at Michigan Technological University have tapped into this additional dimension of sustainability in 3D printing. The group was able to dramatically lower the cost of printing materials by recycling plastic using a recyclebot and also through using a more sophisticated plastic resin code system.
Joshua Pearce, lead researcher, said, 'We are creating a new class of material called ethical 3D printing filament, like fair trade coffee.' After cleaning a milk jug and cutting it into pieces, Pearce's group runs the pieces through an office shredder and a recyclebot. The result is plastic filaments that can be used in a 3D printer. Compared to an ideal urban recycling programme that collects and processes plastics locally, this method uses three per cent less energy, and results in plastic filaments that costs US$10 per kilogramme.
Better Labelling of Recyclable Plastics
To be able to turn recycled plastic into 3D printer filaments, one needs to know which types of plastics can and cannot be used. There are many different types of plastics and specific polymers behave in specific ways. The research team found the US labelling system of categorizing plastics into seven categories inadequate to capture these differences. In contrast, the Chinese labelling system consisting of 140 codes is more comprehensive. The research team devised a new resin identification code system based on the more detailed Chinese system of codes. Then they focused on polymers that could be recycled in 3D printing and designed recycling labels that are woven into the design itself. For example, a pencil holder may reveal its secret polymer type as light shines through its bottom. Through the new labels and new code system the researchers hope to make recycling plastics for 3D printing a widespread practice.
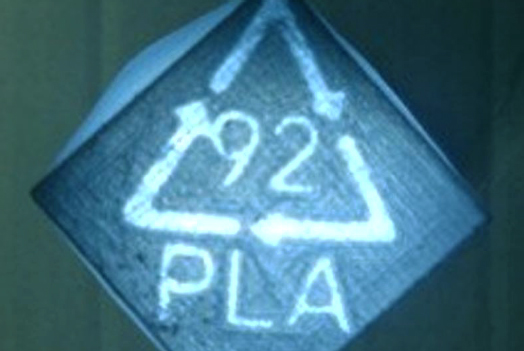